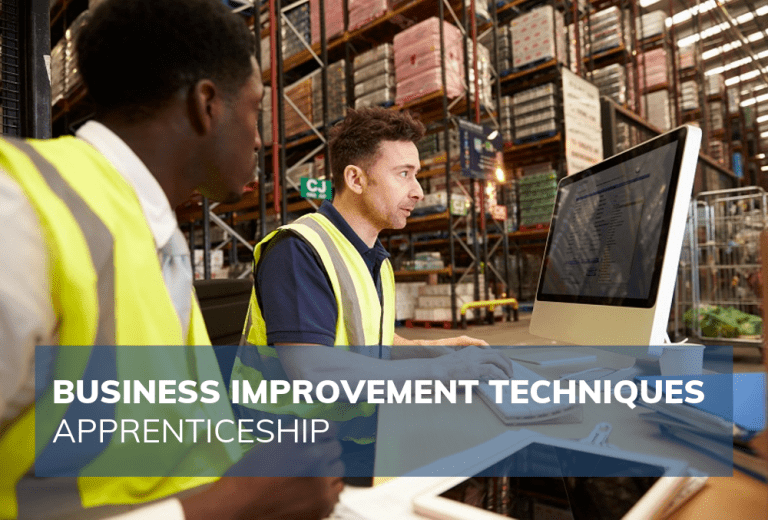
At TRS Training Ltd we go further in fully understanding what it is that our employer clients want to achieve from their training. We work as their partner in delivering on that vision, developing stronger employees who work well as individuals and as part of a team.
Why TRS Training?
We are a market leader in the field of employee development and have delivered our bespoke Business Improvement Techniques training to a growing number of major employers.
Our success is built on delivering proven results for employers including increases in productivity and cost savings.
Our Trainer Assessors have relevant industry experience. Through a balance of classroom and workplace training they teach the techniques which enable employees to identify and make business improvements.
Employer Benefits
- A leaner, more efficient workplace where costs, variation and waste are reduced
- Improved productivity and performance
- Assisting with employee retention, teamwork and motivation
- Helping your workforce feel valued
- Showing customers and prospects you invest in quality improvement
Employee Benefits
- Acquiring new knowledge and skills
- Recognition through national qualifications
- A career development opportunity
- Improved morale and better job satisfaction
What to expect
- All sessions can be timed conveniently around changing shift patterns or night shifts
- We can re-arrange sessions to avoid busy periods or unanticipated events
- During their training employees work towards National Vocational Qualifications at Level 2 (Intermediate)
- One-on-one sessions at any stage of the training can be arranged for individuals who cannot make a group session due to work conflicts.
- We include individual assessment and development of Maths and English skills where required.
Training in a different class
“Employers value this level and type of training. It provides learners with a greater awareness of how quality improvement processes are applied in practice and gives them an opportunity to impact directly on improving efficiencies in the company.”
Business Improvement Theory & Knowledge (months 1 – 6)
During 10, half day sessions employees learn key theories and develop their knowledge. We use a suitable meeting room or space on site or can arrange this off site if preferred. Classroom sessions incorporate shop floor learning.
Topics
Statutory regulations and organisational safety requirements
- Health & Safety in the workplace
- Workplace accidents and emergency procedures
- Lifting and carrying in the workplace
- Applying good housekeeping and safe working practice in a lean environment
Effective Team Working
- Principles of establishing productive working relationships
- Dynamics of team working and creating effective working relationships
- Use of information in working relationships
- Communicating in the workplace
Workplace Organisation techniques
- Principles and benefits of workplace organisation
- The 5 key steps of workplace organisation
- Principles and application of tagging in the workplace
- Auditing techniques of workplace organisation
- Workplace organisation as a basis for other improvement activities
Continuous Improvement Techniques (Kaizen)
- Principles of continuous improvement deployment
- Identification and elimination of waste in the workplace
- Benchmarking the process
- Applying continuous improvement principles
- Key performance indicating techniques
- Sustaining improvements in the workplace
Contributing to the development of visual management systems
- Principles and benefits of visual management systems
- Using visual management systems in the workplace
Workplace Related Projects (months 7 – 12)
The second half of our bespoke BIT training involves learners identifying and tackling two workplace related projects on Quality, Cost and Delivery. These are undertaken in teams and directly address a gap or inefficiency the learners identify within their workplace processes. The Kaizen techniques are used, with solutions often resulting in cost savings or quality and production improvements.
Assessment
This takes place in the workplace and includes:
- evaluation of performance
- presenting evidence of the 2 Kaizen projects on Quality, Cost and Delivery
- Online and written assessments
- Project reports and observation reports which are collated by our Trainer-Assessors
Each employee develops a portfolio of evidence which demonstrates they can perform at the level described.
Find out more
If you are an employer
seeking apprentices for an existing programme, or want to work with TRS Training to start your own Apprenticeship Programme please call 01744 809010